
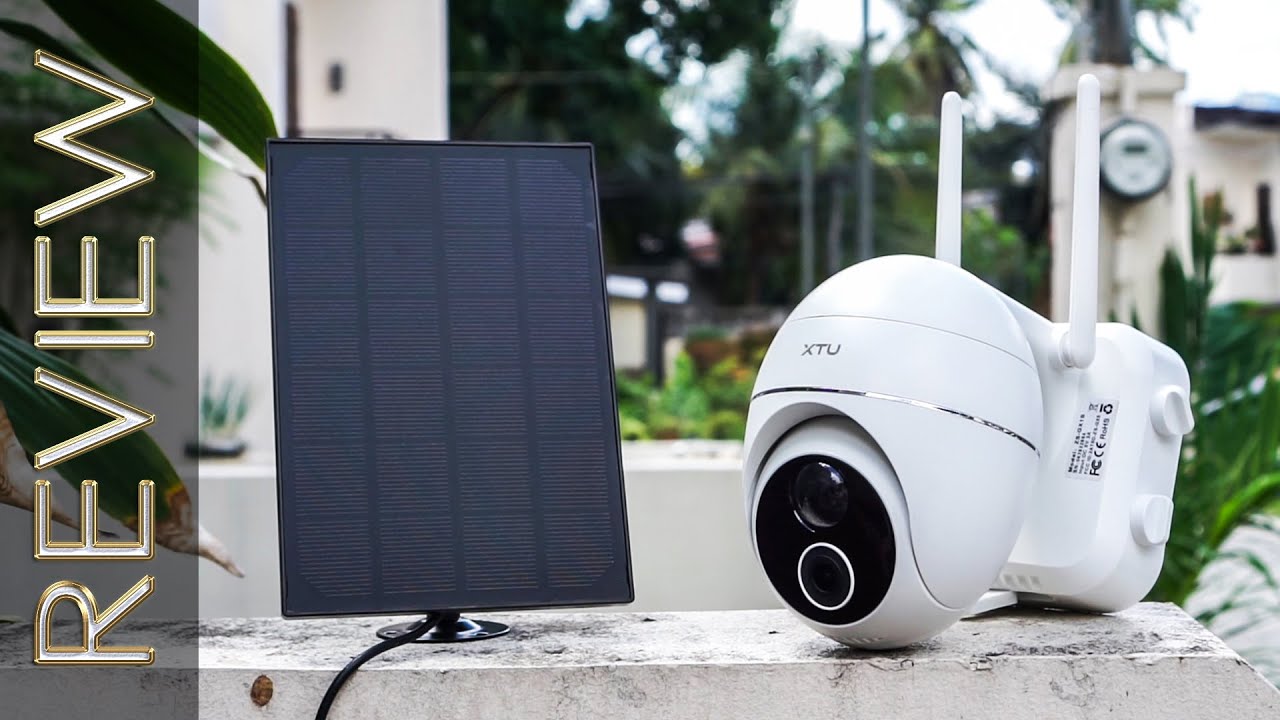
Please look at the picture for the receiving capabilities of the battery guard against the BMMs. Sending data over BLE and WiFi with good antenna capability was an very important requirement. This will result in an adaptation of the housing. IP6x enabling steps are also being performed. There are ongoing works regarding a molded version of the BMMs. Please look at the picture below with a battery guard and two BatMonMinis (3D-printed enclosure) included. Please note that i am developping an own APP for handling the whole data (car battery voltage, cranking voltage, motion sensor signals. For that i implemented some BLE-Services and -characteristics and used the APP in order to compare the battery guard voltage value with those from the BMMs. For the comparison i also used the APP i received when buying the battery guard.

That's why I wanted to compare the battery guard with the BMM system in addition to meeting the above antenna requirements. The antenna signal strength of the battery guard was sometimes poor. I then tested those systems against a battery guard i bought several months ago. I printed some 3D enclosures and installed the PCBs inside.
WIFI SOLAR BATTERY MONITOR UPDATE
Enabling Firmware updates Over the Air -> would enable a remote software update ->highly mandatory.
WIFI SOLAR BATTERY MONITOR BLUETOOTH
Enabling the access to the monitoring system over Bluetooth Low Energy and WiFi.Managing (monitoring/controlling) the auxiliary power supply.Implementation of the motion detection and classification features.Advanced filtering algorithms (adaptive filtering, kalman filtering.Measurement/observation/estimation of stationary (mean battery voltage value.Observation of time depedent calibration parameter.Estimation of calibration constants / Observer algorithms for automatic calibration.Gaining car battery voltage data from operational amplifier.New circuits parts have been tested and propagated onto new plattforms or used to extend older plattforms. The inheritance of tested/approved functionalities was focused. This is mainly due to some circuits parts i imported from some plattforms (developped before) based on last projects. The first PCB production batch consists of 10 items. Please note that the enclosure is realized by two parts. I released the PCB fabrication after the final step of the enclosure design.Ī picture from a version of the whole system (PCB, enclosure) could be seen below. At the end i got a version that would be used for the enclosure production (injection molding). I iteratively printed the enclosure with my own 3D printer and then made some changes on the CAD models. Before sending the PCB gerber files to the manufacturer, i designed the whole enclosure with some CAD tools. I chose an integrative design for this project. For motion detection and sensing, i used a 3DoF inertial measurement sensor with enhanced low power capabilities.Īn overview of the PCB schematic could be read from the picture below. Good antenna requirements have been fulfilled by using a 3D antenna with a matching circuit between the RF unit of the MCU and the antenna itself. The underlying transfer function has been calculated by using some electrical circuits theorems. The enforced hardware bandwidth (~ 500Hz) could be read from the bode diagramm below. Enforcing a good noise rejection (high frequencies) by enabling the sensing of cranking sequences at the same time, ends up in the design of some hardware filtering stages. I designed and developped a four layer PCB accordingly to achievable requirements.
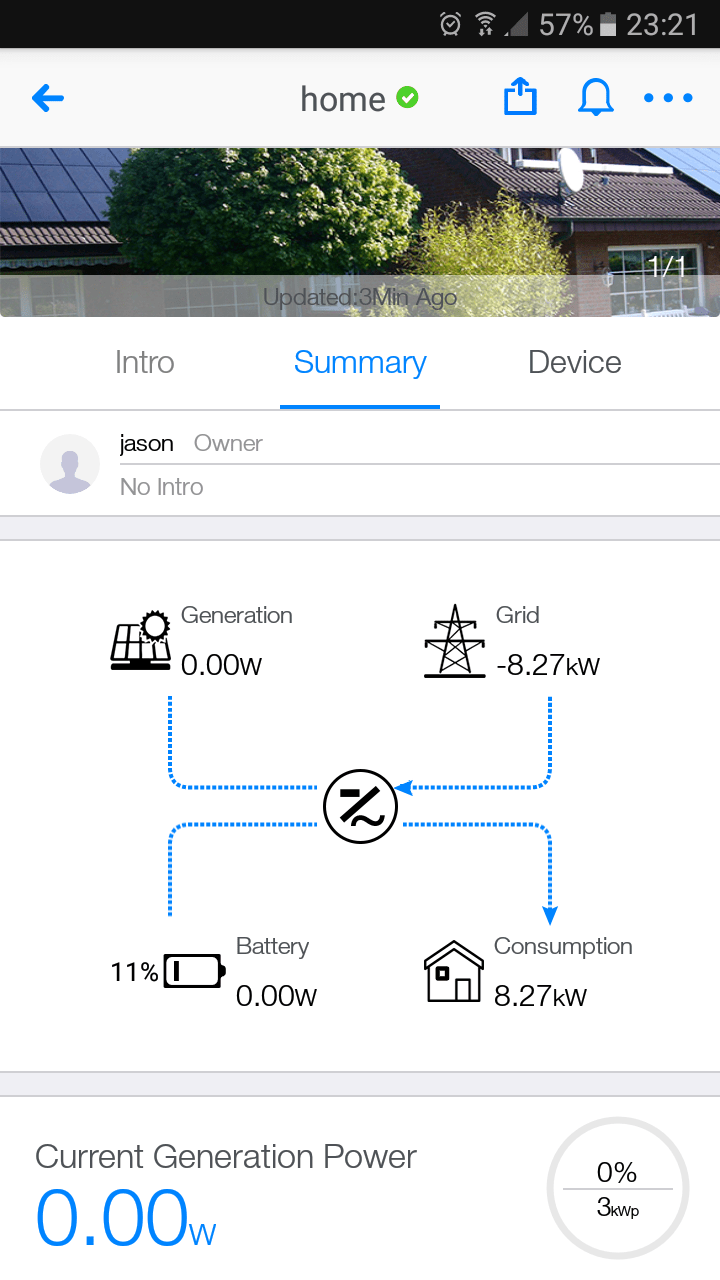
I divide the whole system into the hardware (PCB, mechanical enclosure. I processed and refined those requirements and iteratively generated a list of achievable requirements.
